O-ring, is a round (O-shaped) section of an elastomeric loop used as a mechanical sealing element. They are designed to create a seal in the interface, fit into a groove and to be clamped during assembly between two or more parts. It may have a relative movement between a part and an O-ring (for example, rotating pump shafts and hydraulic cylinders) as a common static. Moving joints generally do not require O-ring lubrication to reduce wear. This is usually achieved by liquid closing down. Since O-rings are one of the most popular sealing elements used in machine design, they have reliable and simple mounting requirements to make them cheap and easy to mount. They can withstand the pressure in dozens of megapascals (thousands of psi). In some cases, O-rings are used in conjunction with backup rings.
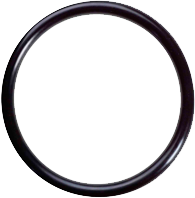
A predictable deformation is available for successful O-ring joint design O-ring. Requires rigid mechanical installation. Sealing is designed for a contact point between the O-ring and the gasket faces. This, allows the O-ring to provide a high local stress possible, including high pressure without exceeding the yield strength of the body. The flexible nature of the O-ring material accommodates defects in its mounting parts. O-ring is in standard size and can be used in a large number of materials. Manufacturers or reference books are the data source for application and processing for assembly. O-ring is one of the most common and important elements in machine design.
O-ring selection is based on chemical compatibility, application temperature, sealing pressure, lubrication requirements, quality, quantity and cost. Typical O-ring materials: Nitrile (NBR or Buna-N), Silicone (VMQ), ® Fluorocarbon (Viton, FKM), perfluoroelastomer (Kalrez ® (FFKM), Fluorosilicon (FVMQ), Ethylene Propylene (EPM, EPDM, EP, EPR), Neoprene (CR, Chloroprene), Polyurethane (AU, EU).